One of the most significant challenges for a company in the food industry is handling raw materials and perishable products. Due to their limited shelf life, there's very little room for error in their management.
Advanced inventory management: Tracking the expiration dates of perishable products to ensure they are sold before reaching their expiration.
Production planning: Strategizing production to align with customer demand and prevent surplus perishable products.
Quality control: Monitoring the quality of perishable products to ensure they are sold in optimal condition.
Interested in learning how to use Odoo to manage your perishable product company?
Keep reading
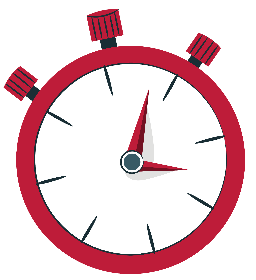
Expiration dates play a crucial role when managing perishable products in your company. By configuring the expiration date field for perishable products, a company like El Horno de la Abuela Bakery can track product expiration dates and take actions to sell or donate products nearing their expiration. You can implement three configurations in your Odoo instance as well.
A. Configure the expiration date field for perishable products.
B. Use the Manufacturing module to align production with customer demand.
C. Track the quality of your perishable products using the quality control module.
We're sharing the process along with additional recommendations so that your company can grow like El Horno de la Abuela Bakery—without compromising product quality or profitability.
A. Configure the expiration date field for perishable products: This enables Odoo to track product expiration dates and generate alerts as expiration approaches.
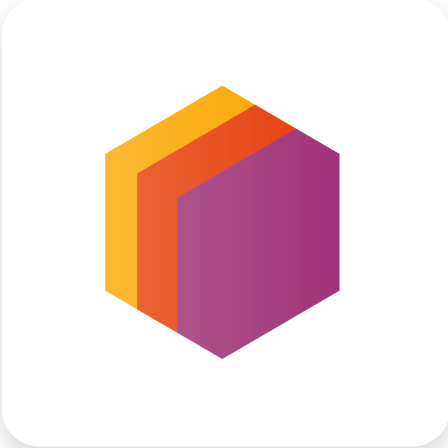
To set up the expiration date field for perishable products in Odoo, follow these steps:
Once the expiration date field is configured, Odoo will start tracking the expiration dates of perishable products. When a product's expiration date approaches, Odoo will generate an alert so that your bakery staff can take action to sell or donate the product before it expires.
Here are some additional tips for configuring the expiration date field:
Set a realistic number of days for the shelf life of your perishable products. This ensures products are sold before they expire.
Ensure all perishable products in your inventory have their expiration dates correctly configured. This prevents the sale of expired products.
Use expiration alerts to stay informed about your perishable products' expiration dates. This helps you take timely actions to avoid losses and waste.
B. Use the Manufacturing module to adjust your production in line with customer demand: This prevents overproduction of perishable products.
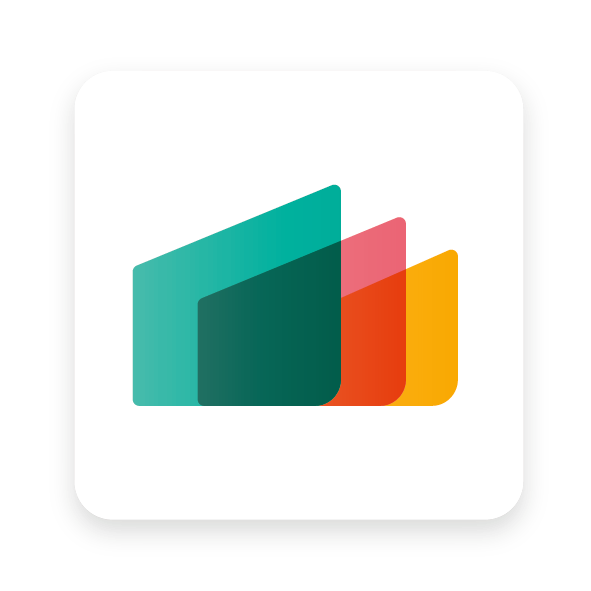
To use the Manufacturing module, follow these steps:
In the Create Master Production Schedule window, provide the following details:
Product: The product you want to plan for.
Start Date: When you want production to commence.
End Date: When you want production to conclude.
Quantity: The amount of product you want to produce.
Odoo will use the provided information to generate a master production schedule. This schedule indicates the quantity of product you should produce in each period to meet customer demand.
Here are some additional tips for using the Manufacturing module:
Regularly update the master production schedule to reflect changes in customer demand. This ensures your production aligns with the current demand.
Utilize production planning reports to analyze your production and identify ways to improve. These reports help you identify areas where efficiency can be enhanced and excess can be avoided.
By following these steps, you can use Odoo's Manufacturing module to efficiently manage your production and prevent overproduction of perishable products.
C. Use the Quality module to track the quality of your perishable products: This ensures products are sold in good condition.
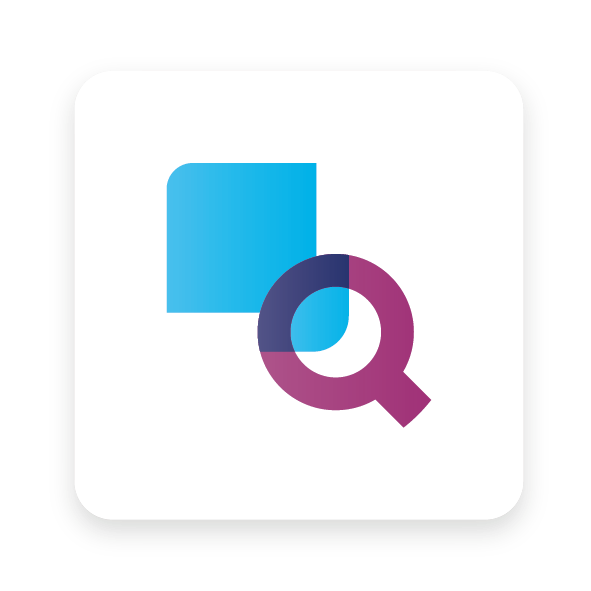
Odoo's Quality app allows food industries to monitor the quality of their perishable products. This ensures products are sold in good condition, leading to satisfied customers.
To use the quality control module, follow these steps:
Name: The name of the inspection point.
Type: The type of inspection point.
Description: A description of the inspection point.
Specification: The specification for the inspection.
Method: The quality control method.
Responsible: The person responsible for the inspection point.
Once an inspection point is created, you can assign it to a production or inventory operation. This allows you to perform quality controls on perishable products at specific points.
Here are some additional tips for using the quality control module:
Create inspection points for all crucial aspects of perishable product quality. This ensures products meet quality standards.
Assign inspection points to appropriate production and inventory operations. This ensures quality controls are conducted at the right times.
Train your staff on inspection points and quality control methods. This ensures effective quality control procedures.
By following these steps, you can use Odoo's quality control module to guarantee your perishable products are sold in good condition.
El Horno de la Abuela Bakery and other successful food companies use the Quality Control module to:
Inspect product appearance before sale, checking for correct size, shape, and color.
Taste-test products before sale, ensuring the correct flavor and absence of staleness or spoilage.
Monitor product temperature before sale, verifying proper storage conditions.