When having an online or physical retail store, the main objective is always to maintain an optimal inventory both in the store and in the warehouse, as managers we understand that it is not an easy task to perform and that correct records of what comes in are needed, leaves or moves inside the warehouse.
In this blog post we will talk about the risks that can arise from having an inventory for your online or physical store, as well as a tool that you can use to have greater control.
What problems can exist within inventory management?
Managing a warehouse is not easy at all, since there is usually a large amount of money invested in the inventory that needs to be sold, not having proper control over it can lead to losses that at the end of a year will be gigantic.
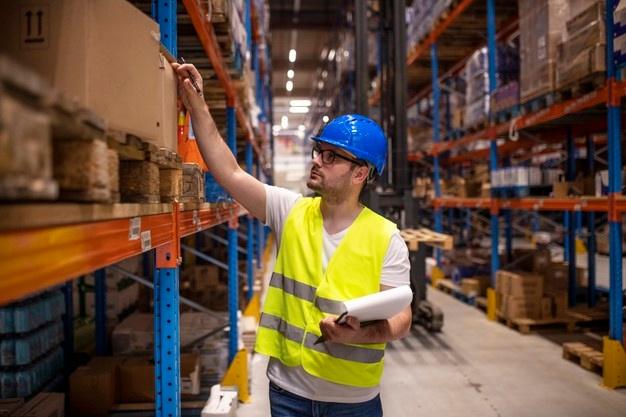
Theft due to poor inventory control
Losses due to human error
Using systems such as spreadsheets to keep track of inventory could cause loss of information about products found in stores or warehouses.
It can be due to common mistakes where a collaborator accidentally deletes information or the file is not saved correctly. It may also happen that the spreadsheet file does not open on other versions of the operating system.
Damage to your products
In a warehouse, there are always high and low-value products, therefore, the control and periodic review of these products are not the same for your high-value inventory as it is for low value, according to the Pareto principle or rule of 80/20, 20% of your products generate 80% of the merchandise movements, while the other 80% of the other products generate the remaining 20% of the merchandise movements.
To maintain proper control, you can use the ABC method that classifies your inventory into three levels, where the items that occupy 20% of your inventory have a more frequent control and inventory than the other items.
If you are interested in learning more about the ABC method, you can visit our blog on How to control your inventory efficiently?
Perishables
Wrong forecasts
Odoo Inventory
To maintain a correct inventory and avoid the aforementioned problems, the use of an inventory management system that facilitates the administration of your stock in a simple way should be prioritized. With Odoo Inventory, you can:
Have a fully automated replenishment.
Handle the management of multiple warehouses.
Generate extensive traceability to know where your products are throughout your supply chain.
Clear and complete reports of each of your warehouses.
It allows you to compare the physical count with what you have in the system through reports that you obtain from different locations or warehouses
Know stocks in real-time.
Connection with the other Odoo modules, including Sales and Purchases. While you move the purchase, sale, or manufacture in Odoo, the inventories are moved in real-time and are costed according to the methods that have been configured: Automatic or manual.